
Polylactic acid (PLA) resins
are made from 100% renewable resources such as corn (maize), sugar beet, and
sugarcane. A clear thermoplastic, it is fully compostable and biodegradable but
has properties very similar to petroleum-based resins that are converted into
thermoforming sheet. PLA resins are aliphatic polyesters and they provide cost
and performance benefits that are competitive with petroleum-based packaging
materials and fibres. They are widely available commercially and are produced
on an industrial scale, with proven applications on the consumer market.
PLA
sheet for food packaging, including trays for baked goods, fruits, and
vegetables, can be produced without any major equipment or tooling
modifications.
Thermoformed parts made of PLA have clarity
comparable to those formed in OPS and PET. This characteristic, combined with
its temperature requirements for product storage, makes thermoformed PLA
particularly suitable for food packaging trays for baked goods, fruits, and
vegetables, along with medical packaging. It is being used in more applications
as the properties of the material are progressively modified. PLA's performance
benefits include excellent gloss, transparency and clarity; very good flavour
and aroma barrier properties; and easy shaping, printing and embossing. The
material's rigidity can translate into lighter packaging and also offers the
potential for more disposal options than conventional packaging.
As a plant-based material, production of
PLA containers results in a 60% reduction in greenhouse gases and 50% less
non-renewable energy use compared to traditional plastics like PET and PS,
according to leading suppliers.
The demand for PLA packaging is being
driven by eco-conscious retailers such as Wal-Mart. Thermoformers are often
less eager to run PLA sheet because of its higher cost and it's particular
handling and storage requirements. However, it runs well in cut-in-place
thermoforming systems and can also be manufactured using tunnel-heat,
plug-assist set-ups.
Manufacturers of thermoformed products
who are considering switching to PLA can run it without any major modifications
to their equipment or tooling. However, there are some important considerations
that need to be addressed in order to achieve a successful switch from traditional
materials like oriented PS and PET.
Special Handling and Storage
PLA sheet used to be brittle at room
temperature and required special handling and storage considerations. While
this continues to be true with some types, many advances over the past few
years have improved overall material characteristics. Previously, neither the
sheet nor the finished product could be stored at temperatures above
All of JINHONGSHENG Thermoforming
Equipment’s testing on PLA has been completed with a contact heat, cut-in-place
thermoforming system. This equipment permits all heating, forming, and cutting
of the material to be performed in a single station using compressed air,
without the need of a pre-stretch plug or vacuum.
PLA has a low forming temperature,
compared to petroleum-based plastic sheet. Platen temperature must initially be
set at
Mould temperature setting depends on the
desiJINHONGSHENG. If the tool has bar locks, setting the temperature at
approximately
Processors should always keep in mind
that different PLA blends will behave in different ways during thermoforming.
Different types of blends from different suppliers may require completely
different process parameters. Overall, the material's cycle times are
consistent with those of PET and OPS.
After being subjected to thermoforming
and then being returned to room temperature, the skeletal waste web of PLA gets
very brittle and tends to break easily. This presents difficulties in
transporting the web; consistent tension control, large rollers and a minimal
angle when entering the transport rollers will help prevent breakage.
Once PLA has been heated and stretched
through the thermoforming process it loses some of its brittleness. Wall
thickness in products can be reduced while still retaining product strength,
and the formed parts are suitable for automatic stacking immediately upon
leaving the thermoformer.
- Welcome to visit our Stand D82 in VietnamPlas Fair from Oct.,3th-6th, 20192019.09.25
- Congratulation: our new factory starts construction!!!2018.08.19
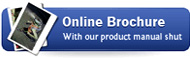
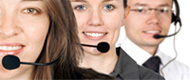
Cell: 0086-137 1993 2305(whatsapp/viber/wechat)
Fax: +86-754-82480335
MSN:
SKYPE: jhsmachinery
E-mail: market@jhsmachinery.com
Contact Person: Jack from JHS Machinery
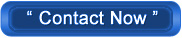