
What is thermoforming?
Thermoforming is a technique that
involves placing a sheet of thermoplastic on a frame to heat it, in order to
soften it.
This takes
advantage of the material’s ability to reshape itself without breaking as it
takes its new form with the help of a mold. The residual air between the plate
holding the mold and the hot sheet is then removed by vacuum.
In this way,
the sheet takes on the shape of the mold and, after cooling, the desired part
has been obtained.
How is it useful?
It is possible to achieve many different finished products with the use of thermoforming. Thermoformed products combine resistance, light weight, transparency, translucency, opacity and color, which make them indispensable in many sectors such as transport, packaging, sports equipment, medical and surgical equipment or any product of industrial design.
What are the advantages of
thermoforming?
The
accessibility of thermoforming is, without a doubt, one of its great
advantages. The initial investment is economical, the production of small
orders or complex pieces can be very affordable since the cost of equipment is
low and its durability is remarkable.
Modifications
or alterations to the equipment can be made easily, which offers a maximum of
possibilities. Production times are short as the development of prototypes and
the fabrication of the molds is not difficult.
The
contribution of technology in the supply of plastics, equipment and molds, as
well as the integration of complementary treatments, allow for precise finished
products with excellent definition. All of this helps to reduce the work which
has a direct effect on production costs.
Here are
some pertinent questions to ask before you begin your project:
· What will be the ultimate use of your part?
· In what environment will it be used?
· Will it be used indoors or outdoors?
· Does it need to be supple or rigid?
· What type of finish do you want on the
surface?
· What are the dimensions of the finished
product?
·What is the desired thickness?
·Does the part need to have specific
mechanical, chemical or thermal properties?
·Does the part need to be dimensionally
stable?
· Will the part be subjected to abrasion or
impact?
· Does the part need to comply with any safety
standards for flammability, food or other legal requirements?
· Do you have a sample of your part?
· Are there any existing drawings, sketches, 2D
or 3D of your part?
· What will the annual volume, the quantity per
order and the frequency of your orders be?
All
of these points will influence the choice of the most suitable material, the
type of molds and, by extension, the manufacturing cost.
- Welcome to visit our Stand D82 in VietnamPlas Fair from Oct.,3th-6th, 20192019.09.25
- Congratulation: our new factory starts construction!!!2018.08.19
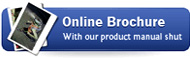
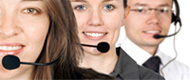
Cell: 0086-137 1993 2305(whatsapp/viber/wechat)
Fax: +86-754-82480335
MSN:
SKYPE: jhsmachinery
E-mail: market@jhsmachinery.com
Contact Person: Jack from JHS Machinery
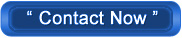